07 Aug Brand Interview: Amano Kouya Indigo Dye
It was a breezy autumn afternoon when we travelled to the small town of Hirose where we visited Mr Takashi Amano, the 5th generation of Amano Kouya Indigo Dye (天野组屋) for a chat.
We were warmly greeted by Takashi-san who showed us his workshop, surrounded by indigo dye-vats, we could not help but breathe in a sharp scent. We later found out that it was the smell of fermentation from the plants that are used to produce the dye. One cannot help but also notice his fingernails which were also dyed in indigo, a result from his daily dyeing works.
Our interview started as we settled down in his workshop to learn and understand the importance of protecting this Japanese tradition:
J’MARKET: Please tell us how Amano Kouya started.
Takashi-san: Amano Kouya was founded in 1870. The first generation owner opened his own business after training at another indigo dyeworks in Hirose-cho. Our current location is where we built the “Amano Dyeing Workshop.” As of year 2019, Amano Kouya has been opened for 149 years.
J’MARKET: So how did indigo dye originated in Japan?
Takashi-san: It is not clear when exactly indigo dyeing came to Japan. However, the oldest indigo-dyed cloth in Japan is kept in the Shoso-in treasure house of Todai-ji temple in Nara, so it is clear that indigo was already here in the Nara period (AD 710 to 794). In the twelve level cap and rank system for imperial court officials of the time, indigo was ranked second only after violet, meaning it was a noble colour that commoners were not permitted to wear.
“People loved strong, beautiful indigo-dyed products”
In the Edo period (AD 1603 to 1868) when commoners were finally allowed to wear indigo, indigo-dyed products spread to every corner of life in the blink of an eye. The reason for this was its functional beauty. In the process of being dyed over and over, indigo-dyed threads receive a surface coating that makes them stronger. Supplies were more limited at the time, and it was very important to people that they be able to use a kimono for a long time once it was made. People loved strong, beautiful indigo-dyed products.
[Mr Takashi Amano and the indigo dyed-vats]
J’MARKET: Are the equipment and machinery you have now original creations?
Takashi-san: Half of the 16 indigo dye-vats filled with indigo dye are originals from when the this place was founded, and have become something like the guardian gods of Amano Kouya. Each indigo dye has a different brightness: very dark, slightly dark, slightly light, and very light.
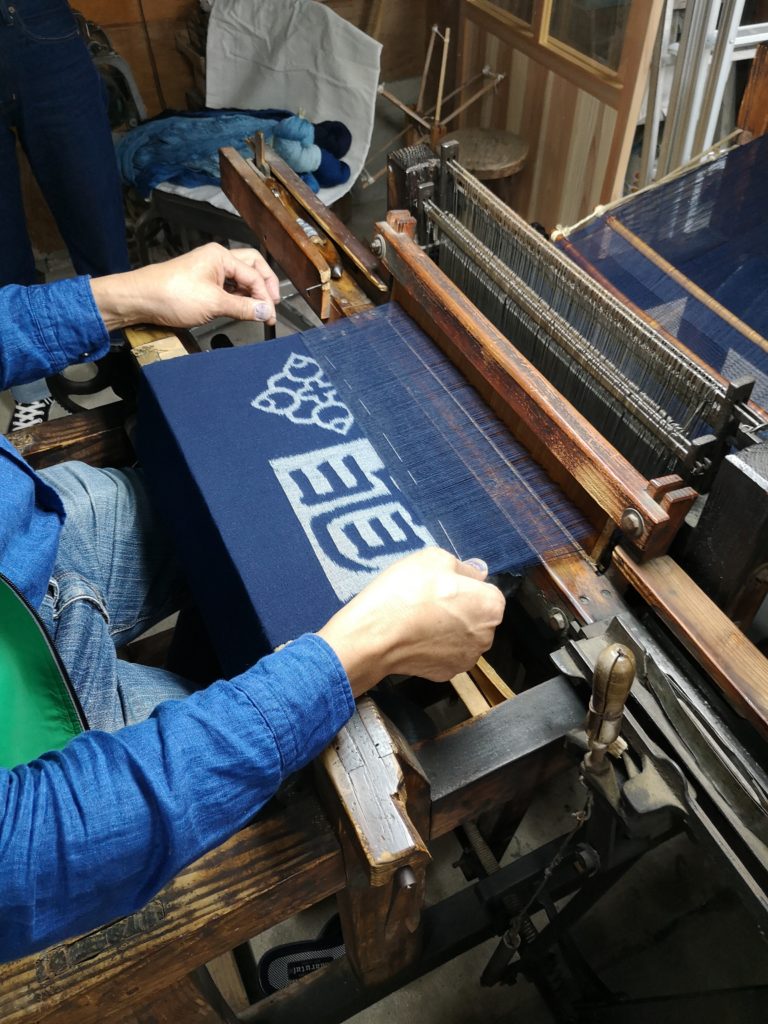
[Takashi-san’s father demonstrating weaving on a century-old machine]
Takashi-san: The main ingredient for indigo dye is a substance similar to humus called “sukumo”, made from fermented Japanese indigo leaves. This sukumo is fermented day and night in an alkaline solution with ash mixed in to make indigo dye. Materials are dyed in a beautiful indigo blue with a little help from the yeast living in indigo dye-vats without the use of mordants (a substance used to bind the dye and fabric together). Fermentation does not always go well, even if the ingredients are mixed and kept at the right temperature according standard for the process, so it can take anywhere from 10 days to 1 month to finish. Jobs like this that don’t go exactly as described in a manual and it relies on the intuition and senses of the craftsman.
“Jobs like this that don’t go exactly as described in a manual and it relies on the intuition and senses of the craftsman”
It is an important responsibility of the craftsman to master not only dyeing skills, but also to keep indigo dye-vats at the right temperature for fermentation at all times and add the necessary amount of wheat bran and maltose syrup to feed the yeast. The beautiful indigo “flowers” (indigo coloured bubbles) that float to the surface of the liquid are a sign that the yeast is hard at work. If craftsmen cannot do this, then they cannot indigo-dye materials.
Takashi-san’s father demonstrated how they check the fermentation process – with his tongue! No equipment or tool was necessary as just a taste of the indigo dye could tell him if the dyes were at the right stage.
J’MARKET: How long does it take to dye a single product?
Takashi-san: The time it takes differs depending on the desired shade. Lighter shades can be finished with a single dyeing, while darker shades must be dyed darker and darker by repeating the process of first dyeing in light indigo dye, then dyeing in dark indigo dye. This process makes for deep, rich shades. Although it also varies depending on the season, lighter shades take 3 or 4 days, while darker shades can take nearly a week.
J’MARKET: How do you incorporate traditional skills into this modern day and having it stand out?
Takashi-san: Sometimes I do this by trial and error considering what is demanded by the era and the customers, but this does not go well if i cannot put my heart into it. I just feel better making things that I would like to use myself.
“There is a certain palpable power in the things we make which mass produced items will never have”
J’MARKET: What would you like to tell customers buying indigo-dyed products?
Takashi-san: I just want people to buy something that has a colour they like or a pattern they like, without worrying about anything too complicated like traditional crafts. I think people will either recognise the craftsmanship or not in an instant, and I’m really happy when people buy products that I was excited to make. When the maker is happy, this will show in the product itself. There is a certain palpable power in the things we make which mass produced items will never have.
As there are fewer and fewer craftsmen who have the necessary seasoned skills, it is becoming more crucial to support people like Takashi-san to allow him to continue his craft for future generations.
Related Article: 5 Facts About Japanese Indigo Dye
Sorry, the comment form is closed at this time.